12-layer High-speed Backplane
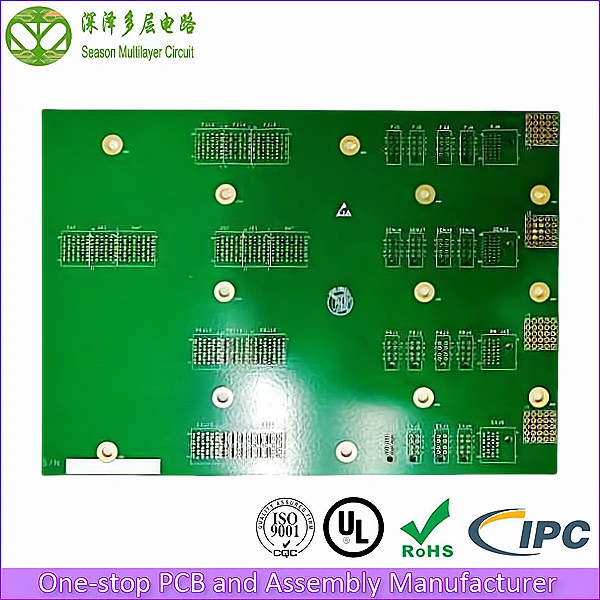
High-speed Backplane
Layer Count: 12L
Material: FR4 IT200LK Tg200
Material: 2.4mm
Panel Size: 420*150mm/1
Outer Layer Copper Thickness: 1 OZ
Inner Layer Copper Thickness: 1 OZ
Min Via Diameter: 0.25mm
Trace Width/Spacing: 5/5mil
Surface Finish: ENIG2U’’
12-layer high-speed backplane PCB for automotive central control systems, serving as a neural hub product that interconnects various vehicle systems.
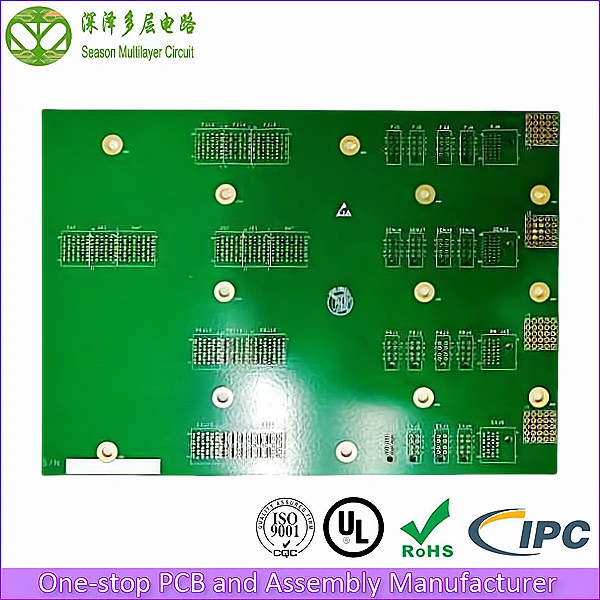
The Role and Applications of 12-Layer Automotive High-Speed Backplane PCBs in Modern Vehicle Design
Introduction
In automotive design, high-speed backplane PCBs (Printed Circuit Boards) play a crucial role in ensuring vehicle performance, safety, and efficiency. As vehicles become more advanced, integrating complex electronic systems, the demand for high-performance PCBs has grown significantly. This article explores the definition, functions, and applications of 12-layer automotive high-speed backplane PCBs, highlighting their importance in modern automotive manufacturing.
1. Definition of Automotive High-Speed Backplane PCBs
An automotive high-speed backplane PCB is a structural and electronic component that serves as the backbone for interconnecting multiple vehicle subsystems. Unlike traditional PCBs, a 12-layer high-speed backplane is designed to handle rapid signal transmission, ensuring seamless communication between critical automotive systems such as:
- Infotainment systems
- Advanced Driver-Assistance Systems (ADAS)
- Engine Control Units (ECUs)
- Sensor networks (LiDAR, radar, cameras)
The term “high-speed” refers to the PCB’s ability to support fast data transfer rates, minimizing signal loss and electromagnetic interference (EMI). These backplanes are typically installed in key areas of the vehicle, including the trunk lid or central control panel, where they facilitate robust electrical connections.
2. Key Functions of Automotive High-Speed Backplane PCBs
2.1 Enhancing Structural Rigidity and Strength
A 12-layer backplane PCB contributes to the vehicle’s structural integrity by reinforcing the chassis and body frame. Its multi-layered design distributes mechanical stress, improving durability under high-speed driving conditions and rough terrains.
2.2 Securing Electrical and Aesthetic Components
The backplane provides a stable mounting platform for:
- Interior & exterior trim components
- Lighting systems (LEDs, headlights, taillights)
- Control modules (HVAC, power windows, seat adjustments)
By ensuring secure placement, it prevents vibrations and misalignments that could compromise functionality.
2.3 Reducing Aerodynamic Drag and Noise
Automotive backplanes are engineered to optimize airflow around the vehicle, minimizing wind resistance and cabin noise. This leads to:
- Improved fuel efficiency (lower drag = better mileage)
- Enhanced passenger comfort (reduced wind and road noise)
2.4 Improving Crash Safety and Energy Absorption
In collision scenarios, the 12-layer PCB’s reinforced structure helps absorb and dissipate impact energy, reducing force transmission to passengers. This is particularly critical for electric vehicles (EVs), where battery safety is a top priority.
3. Applications in Automotive Manufacturing
High-speed backplane PCBs are widely used in modern vehicles, including:
3.1 Electric & Hybrid Vehicles (EVs/HEVs)
- Battery Management Systems (BMS) rely on high-speed PCBs for real-time monitoring.
- Power distribution networks require low-loss signal integrity.
3.2 Autonomous & Connected Cars
- ADAS modules (adaptive cruise control, lane-keeping assist) depend on fast data exchange.
- V2X (Vehicle-to-Everything) communication demands ultra-low latency.
3.3 Luxury & Performance Vehicles
- High-end infotainment systems (4K displays, AI voice assistants) need high-bandwidth PCBs.
- Active suspension systems require rapid signal processing for dynamic adjustments.
4. Future Trends in High-Speed Backplane PCB Technology
As automotive technology evolves, 12-layer high-speed backplane PCBs will see advancements in:
4.1 Lightweight Materials
- Carbon fiber-reinforced PCBs for weight reduction without sacrificing strength.
- Flex-rigid PCBs for compact and adaptable designs.
4.2 Enhanced Signal Integrity
- 5G & mmWave integration for faster in-car networking.
- Advanced EMI shielding to prevent interference.
4.3 Sustainable Manufacturing
- Lead-free soldering & recyclable materials to meet environmental regulations.
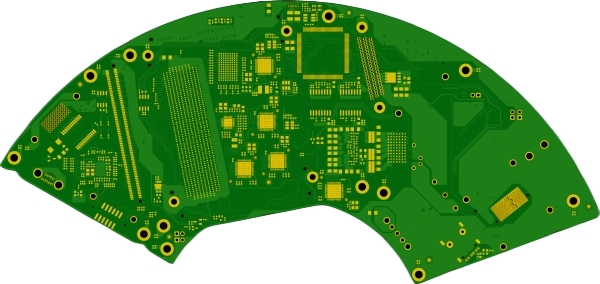
Conclusion
The 12-layer automotive high-speed backplane PCB is a fundamental component in modern vehicle design, influencing performance, safety, and efficiency. As cars become more connected and autonomous, the demand for high-reliability, high-speed PCBs will continue to rise. Automotive manufacturers must invest in R&D and advanced manufacturing techniques to meet these evolving needs, ensuring safer, smarter, and more sustainable vehicles for the future.
By prioritizing innovation in PCB technology, the automotive industry can deliver next-generation vehicles that exceed consumer expectations in durability, intelligence, and energy efficiency.